Guide: Performing Material Takeoff
Togal.AI
|
A takeoff is the list of materials needed to complete a construction project that is determined by a thorough analysis of the construction drawings. The general contractor uses the takeoff to identify an accurate estimate for project costs.
Read further to gain insight on material take off, its role in construction, and how it is implemented by estimators.
Material Takeoffs During the Bidding Process
Before general contractors can submit a proposal for a project, the types and quantities of the materials needed must first be identified. This will ensure an accurate estimation of the material and labor costs associated with installing the materials.
In the construction industry, the material takeoff process or MTO is identified by varying names, such as a quantity takeoff, a construction takeoff, or simply a takeoff. At the fundamental level, a material takeoff aims to provide a comprehensive list of materials, their quantities, and a detailed cost per material required for the project. Often, this excludes tools, equipment, or machinery required for the project.
For large-scale construction firms, the material takeoff process is performed by a team of estimators. The Director of Preconstruction often handles the company's bid calendar and assigns projects to estimators.
The Importance of a Material Takeoff
Inaccurate material takeoffs are the leading cause of delays and cost overruns. Both issues can negatively impact the reputation and profit margin of a construction firm. Resulting in legal disputes and issues of financial responsibility between the owner, general contractor, and the sub-contractors.
An example is the Wembley National Stadium in the United Kingdom which had a cost overrun of 32% and is known for its extreme legal bills. In 2007 during a complicated dispute concerning the roof design, the famous arch, and the groundworks, £1m was spent on photocopying alone. At a sub-trial with only a few issues disputed, the costs were cited as £45 million.
Although the general contractor, won the dispute, they still suffered £2m in losses due to excessive legal fees. Multiplex, the general contractor, was a previously successful and established company of 43 years. The company suffered major damage to its reputation as a result of the high-profile and heavily publicized lawsuit and was subsequently sold.
To ensure projects are accomplished on time, within budget, and with healthy profit margins, it’s important to streamline the takeoff process and ensure its accuracy. This can be achieved through accurate measurements, accurate values, up-to-date plans, and equipping estimators with advanced construction estimating technology.
Material Takeoffs: Measurement Types
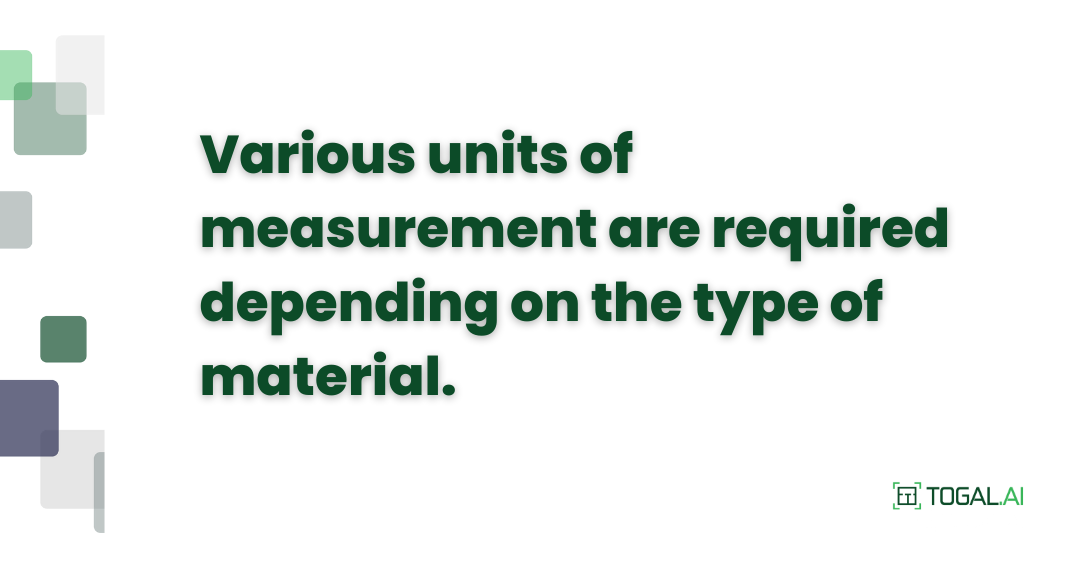
Various units of measurement are required depending on the type of material. Read further to gain insight into some of the standard units.
Count
Counts are used for identifying specific individual items such as light fixtures, outlets, standard wall studs, doors, windows, sinks, bathtubs, showers, parking spaces and more.
Length
Items such as cables, pipes, ductwork, drywall, paint and conduit are measured by length. Depending on the type of material being measured, other dimensions such as the width may also be relevant. Additional length is allotted for elements such as panels, receptacles, and switches.
Area
Surface area measurements are necessary for flooring, sheathing, cladding, plaster, and roofing.
Volume
Measurement of volume is necessary for materials such as concrete, sand, gravel, and asphalt. For example, the measurement can be applied when determining the amount of concrete required to lay the foundation. Volume is calculated by multiplying the length by width by depth to get the cubic yards needed.
Other Measurements and Specifications
Weight
The weight of materials is not always provided in material takeoffs. However, this measurement may be necessary when determining shipping and transportation costs. This is especially applicable for large-scale projects where there are significant costs in transporting materials to the job site.
Material Descriptions
Material takeoffs serve as a reference when ordering materials for a project. Hence, a detailed product description is necessary. For example, when the estimator includes lumber in the list of materials, the size of the lumber and any special treatment required may also be specified. This ensures the right materials for the project are ordered.
Material Takeoff: Three Methods
Initially, two methods are used to complete takeoffs - manual and digital. As the construction industry has evolved, recent technologies such as machine learning and artificial intelligence are being applied to streamline the material takeoff process.
Manual Takeoffs
Manual takeoffs require estimators to look at traditional paper blueprints and calculate the quantities of each material manually. First, the scale of the drawing is identified. Then, colored pencils or markers are used to distinguish between all items and types of materials. Materials and quantities are then entered into spreadsheets or forms to determine the exact material costs for each component.
A manual takeoff is a more traditional way of doing a construction takeoff. It is tedious, requires a lot of manpower and can take weeks and even months to complete.
Digital Takeoffs
Digital takeoffs enable estimators to analyze a set of blueprints and enter the measurements and quantities digitally. Some digital takeoff softwares can also integrate with a bidding or quotation program to combine the two processes.
The downside is that although the standard takeoff software is digital, it can still be labor-intensive and prone to errors. Estimation softwares may have a steep learning curve that can slow team productivity. Extensive manual editing may be needed to fit the requirements of the project. On average, one full-time estimator takes 90 minutes per page to complete an area analysis, a linear takeoff, and an object count.
AI-Powered Takeoffs
General Contractors and their team of seasoned estimators spend 40-60% of their time conducting takeoffs. With a construction takeoff software powered by AI and machine learning, takeoffs can be completed in a fraction of the time. By automating take-offs and producing accurate cost estimates, general contractors are able to shift their focus towards scoping, pricing, and value engineering.
Material Takeoff Process
The exact process for material takeoff varies depending on several factors including the scale of the job and the type of takeoff method used - whether manual, digital, or automated with AI.
The takeoff must quantify all the physical materials required to complete the project, excluding tools and equipment. This includes raw materials such as sand, concrete, and timber. Additionally, this includes prefabricated items such as plumbing pipes, light fixtures, and bricks.
List Materials Required for the Project
Once the blueprints and specifications are thoroughly reviewed, the next step is to make a comprehensive list of all the items required for the project.
Set the Scale
Set or verify the scale on the plans to ensure accuracy. Identify the longest known distance and determine the scale. Measure the distance to verify the measurement and scale within the drawing is accurate.
Define the Quantity of Each Material
Systematically work through the drawings and takeoff each item as they are added to the list. Specify the quantity and unit of measurement when adding the materials as each can impact the cost.
Estimate the Cost Per Material
Apply the estimated cost to each type of material listed. Material costs are often determined by the following:
- Quotes from material suppliers.
- Database of the costs of commonly used materials.
- Construction cost data from local vendors.
- Reference a database like RS Means.
Once the itemized breakdown of costs is complete, the next step is to determine the total material cost for the project.
Allowances for Unforeseen Circumstances
When planning a project, the margin for price fluctuations should be accounted for. Observe what’s happening in the market and consider the impact of supply chain issues and the effect of inflation on material costs.
Allow a buffer for price increases and raise the material costs depending on how the current market trends are positioned to impact them. Doing so ensures that a project remains profitable even if material costs rise.
AI-Powered Software Accelerates the Takeoff Process
To be awarded a construction project and maintain long-term profitability, accuracy and efficiency in conducting the take off is essential.
Manual takeoffs are labor-intensive. Most estimating software claim to achieve fast and accurate takeoffs but still require extensive manual editing.
Togal.AI is an AI estimating software that can automate as much as 80% of the takeoff process. Powered by Artificial Intelligence, the deep learning models enable automatic analysis of drawings. Essentially providing the polygons and counts in seconds.
Outlined below are some of the features that enable Togal.AI to accelerate the takeoff process and give general contractors their competitive edge.
- Deep-Learning Technology - The process of detecting, labeling, and measuring project spaces and objects in the drawings can be tedious and time-consuming. With the use of A.I. and machine learning, Togal.AI can learn and improve from previous drawing analyses.
- 97% Accuracy - Togal.AI eliminates manual and error-prone calculations by interpreting plans with 97% accuracy. The risk of cost overruns is reduced and general contractors can maintain profitable and predictable projects.
- Focus on Value-Generating Activities - With Togal.AI’s efficiency, GCs can shift their focus towards value-generating activities such as scoping, value engineering, and identifying the right trade partners.
- 80% Faster Takeoff - The takeoff process is laborious and could take weeks to months to complete. Togal.AI only takes a few clicks and 3-10 seconds to populate the polygons and object counts necessary for the takeoff. Togal.AI enables estimators to save 90-minutes per drawing.
To know more about how the AI-powered estimation software, Togal.AI, can accelerate the takeoff process, request a demo here.